The Official Ford Mustang 5.0
Price: $69.95
|
Suspension
All 1979-93 Mustangs are assembled with a suspension system based on helical coil springs all around, modified (hybrid) MacPherson struts in front, and a four-link axle locating arrangement with vertical dampeners in the rear. V-8 Mustangs are also factory-equipped with spring-steel stabilizer (anti-sway) bars, front and rear.
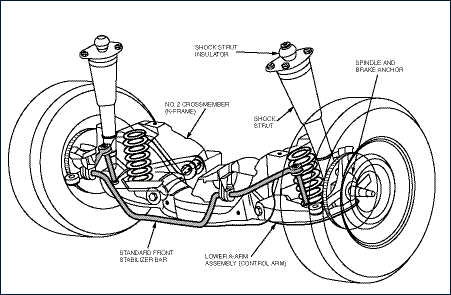
Fig. 29-1. This front suspension is a modified MacPherson strut design. The design uses shock struts with coil springs mounted between the lower arm and a spring pocket in the No. 2 crossmember. The shock struts are non-serviceable and they must be replaced as a unit. The ball joints and lower suspension arm bushings are not separately serviced and must be replaced as an assembly.
The attachment and pivot points for suspension members were precision-located by a process Ford referred to as "hydropiercing." Hydropiercing technology (a pressurized-water cutting process) involves a master fixture that allows simultaneous on-car fitting, cutting, and piercing of suspension components and subframes. This permits assembly to closer tolerances, more precise alignment of components within an assembly, and more efficient material use than assembling and drilling components individually off-car. It also allowed Ford to make minor revisions to suspension geometry during the Fox cars production run.
The suspension system components that Ford fitted to Fox-body Mustangs were selected according to a number of interrelated factors, with the primary consideration among them being the engine used in each vehicle. Component selection could also be determined by a customer"s choice of standard or optional underpinnings. A Mustang buyer was also able to order optional tire sizes that usually made a specific combination of suspension components mandatory at extra cost. And as with all Ford models that the factory manufactured, each individual vehicle"s spring rates were determined by computer calculations that factored in the specific equipment ordered on that car. Note that suspension systems were tuned to suit a particular Mustang"s combination of components by way of spring rates, internal strut and shock valving, and bushing material selected for use with those components. (The term "rate" as used here in discussions of suspension components and systems describes a load-to-distance ratio, typically pounds per inch.)
Pre-1985 Mustangs were offered with three levels of suspension equipment: base, Handling, and TRX. Non-V-8-engined models came with a relatively light-duty standard (base) suspension system. The heavier-duty Handling suspension option and a performance-oriented TRX wheels/tires/suspension package were optional at extra cost. Ordering a V-8 engine or an optional suspension level in pre-1982 models included specific springs, struts, shocks, bushings, steering gear, and a front stabilizer bar, all of which were tailored to the eight-cylinder engine"s weight and power output.
Starting with the 1982 introduction of the Mustang GT, the Handling suspension upgrade (mandatory with the 5-liter V-8 in all models) was also referred to as the GT/Handling suspension. The 1982-84 Mustang GTs and V-8 LXs were also offered with the TRX wheel-tire-suspension option. Both these extra-duty suspension packages added stiffer springs, a larger diameter front stabilizer bar, specific shock and strut valving, firmer suspension bushings, and a rear stabilizer bar.
The (1979-84) TRX option included special TRX wheels and tires, which, in turn, dictated specific engine-dependent suspension system components designed to work together for improved ride and handling characteristics. Although some crossover (quad-shock) components came through on some late-1984 Mustangs, Handling suspension and TRX suspension components were separate and distinct and were not ordered on or normally fitted to the same vehicle. When the TRX option was dropped after 1984, "Special Handling suspension" came to refer to the standard GT suspension and steering gear.
Late in the 1984 model year, many V-8 Mustangs (and some of those equipped with the GT/Handling suspension package) received a new Quadra-Shock rear suspension system. Also in mid-year (1984 1/2), gas-pressurized struts and shocks, multipiece upper front strut mounts, and variable-rate coil springs (with internal rubber damping sleeves) were also fitted for the first time on Mustang V-8 models (as well as on SVO Mustangs and Mustangs ordered with the GT/Handling suspension option). This 1984 1/2 upgrade also included a larger rear stabilizer bar. In addition, the 1984 1/2 rear control arm pivot points were lowered, and the front K-member was slightly revised. This arrangement was carried over for all Mustang V-8 models built for 1985-93.
Both 1993 Cobra models are equipped with specific performance-oriented suspension equipment designed to enhance those cars" unique handling characteristics.
Many of the Mustang"s front suspension components are pictured in Fig. 30-1, page 387.
Tire-Related OE
Suspension Levels
Factory-fitted tire and suspension options were directly related. Mandatory (and often extra-cost) tire or suspension options were dictated by engine size and/or which rubber and/or underpinnings were ordered. All 1983-84 Mustangs ordered with the Handling suspension system were also required to be specified with P205/70R14 tires (which were V-rated for 1984-and-later and H-rated in previous model years). Early-1985 LX V-8s came with Handling suspension as standard, which included mandatory-at-extra-cost P205/70VR14 tires. Ordering the Handling suspension for late-1985-86 non-V-8 Mustangs also mandated the V-rated version of these tires. Ordering P205/70 tires on any 1983-86 Mustang on which they were offered made Handling suspension mandatory.
Handling Characteristics
Although the above-described combinations of Mustang suspension components produce relatively responsive handling, they also allow noticeable body roll and a relatively harsh (sixties musclecar-style) ride. In production form, these combinations leave a lot to be desired in terms of performance. The Mustang"s worst handling traits manifest themselves during hard cornering, acceleration, and under braking.
Near its handling performance limits, a stock Mustang"s suspension system is actually restricted by the architecture of the car"s unitbody construction. Assembled with the same basic suspension members used in Ford"s late-seventies Fairmont line, the Mustang"s standard front suspension geometry produces excessive positive camber and too little caster when cornering. The rear suspension design and its very soft springs are known to result in inadequate rear axle control. This becomes most pronounced at speed and/or under power or hard braking, particularly on uneven surfaces. Twist from the 5-liter V-8 multiplied through these cars" relatively low first gear can also overcome the rear suspension to produce axle tramp (wheel hop) on hard starts.
On post-intro (1982-and-later) Mustangs, handling and control refinements were made through high spring, damper, and bushing rates and oversized tires. But this combination produces a harsh ride, especially on uneven surfaces.
|
Front (inches) (2) |
Rear (inches) (2) |
||
---|---|---|---|---|
Year |
Jounce |
Rebound |
Jounce |
Rebound |
1979 |
3.50 |
3.50 |
3.31 |
4.77 |
1980-82 |
3.66
|
3.34 |
3.41 |
4.54 |
1983 |
3.09 |
4.99 |
||
1984 |
3.20 |
4.88 |
||
1984 1/2-86 |
3.58 |
3.42 |
3.25 |
4.63 |
1987-88 |
3.05 |
4.66 |
||
1989-91 |
3.24 |
4.64 |
||
1992 |
2.90 |
4.81 |
||
1993 (3) |
2.90 |
4.81 |
||
1. Specifications are for the heavy-duty GT/Handling suspension system (standard with V-8s). 2. Travel distances are measured at the wheel. 3. Travel is shown here for GT and LX 5-liter models only. The 1993 Cobra R-Model has approximately .75 inch less front suspension travel than other 1993 V-8 Mustangs. |
||||
TRX
Introduced for 1979, Ford"s TRX option involved a select combination of suspension equipment, specific wheels, and unique Michelin tires. It also involved special spring and shock rates and specific stabilizer bar sizes (all for increased roll stiffness), engineered to complement the exclusive TRX tire-and-wheel combination. The high cornering forces that early V-8 Fox Mustangs equipped with the TRX system were able to generate often made carburetor modifications necessary to compensate for fuel slosh. TRX tires are discussed in Chapter 32.
Priced according to the model on which it was ordered (and sometimes according to the engine with which it was ordered), the TRX system was offered on 1979-84 Mustang and 1979-85 Capri models. It was standard on the 1979 Pace Car and was also included with the 1979-81 Cobra packages. It was also offered on 1981-83 Fairmonts and Zephyrs.
Suspension Bushings
Most Mustang suspension components (like the shocks, struts, springs, control arms, and front stabilizer bar) are carried on the car on bushed connections. Bushings are used at multiple mount and pivot points to fine-tune the suspension system"s ride characteristics, for NVH control, and to isolate metal-on-metal contact points. Unfortunately, most OE bushings are considered too compliant for serious performance service.
Bushing materials (in all OE applications) are described comparatively by the use of durometer numbers. Expressed in a range from 1-100, durometer ratings are graded from softest to hardest. The more load required to cause a bushing to deflect a measured amount, the higher that bushing"s durometer number. Production bushings tend to have durometer ratings between approximately 50 and 66.
Replacing rubber bushings with polyurethane (plastic) replacement bushings can improve handling without producing objectionable ride characteristics. "Poly" bushings are harder than OE rubber, and their limited compliance transmits load inputs from the wheels to the suspension (and the chassis/body) quickly and directly. Suspension components react more rapidly to both road and driver inputs because compression slack in the bushings is minimized.
Without the shock-absorbing properties of more compliant rubber compounds, urethane bushings produce a noticeably harsher ride. And although polyurethane bushings will not deteriorate in hard use as rapidly as rubber bushings, the shock loads they transmit can promote deterioration of the inflexible structures on which they act. Poly bushings are also noisier in operation than OE bushings, but they can be treated with marine grease or soap to help quiet their action, and for ease of installation (in the arms and in the car).
For some applications, the aftermarket also offers solid-metal replacement suspension bushings. But because of their extremely harsh ride characteristics, they are suggested for competition use only. Some hard-rubber replacement bushings are also available from FRPP.
Front Suspension
Common to all Fox-platform vehicles, the Mustang"s front suspension system is based around coil springs with modified MacPherson struts. The front suspension system is tied to the rest of the car mainly via the K-frame. The K-frame carries the lower control arms, which carry the steel lower ball joints. The configuration of this main crossmember evolved through a series of relatively small revisions over the fifteen model years it was in service.
All 1984 1/2-and-later V-8 Mustangs were originally fitted with gas-charged front struts. When Ford fitted 1987 Mustangs with revised struts and spindles, the Fox cars gained 1/2 inch additional suspension travel and more camber for improved tracking at speed. (The spindle revision produces the camber; the strut increases the travel.) A front stabilizer bar was always standard Mustang equipment.
The 1993 Cobra R-Model uses a triangulating engine bay brace between the strut towers and the firewall as well as an undercar X-brace that ties the K-frame to the unitbody structure at points fore and aft of the K-member.
Ford refers to the Fox bodies" front suspension arrangement as a single-arm system. Disadvantages include impact harshness and difficult-to-regulate nosedive on hard braking.
K-Frame
The K-frame is a stamped-and-welded steel bolt-in front subframe crossmember. The K-frame is also referred to as the K-member, engine support cradle, or "number two" crossmember. The "K" designation describes the assembly"s basic shape. Transversely oriented, the K-frame is attached to the Mustang unitbody"s forward subframe rails by eight fasteners. The production K-frame carries the motor mounts, steering rack, front springs" upper pockets, and lower control arms.
Most Mustangs built with 4.2-liter and 5-liter V-8s, the 3.8-liter V-6 and with the (non-SVO) 2.3-liter four-cylinder engines share the same basic K-frames. Mustangs built with the (3.3-liter) inline six-cylinder engine (late 1979 through 1982) use a different K-frame configured for that engine"s unique motor mount arrangements.
In 1987, the V-8 Mustang K-frame was redesigned with revised pickup points for the lower control arms. This revision improved overall suspension geometry, produced more favorable caster, and allowed a little more tire clearance up front. The 1984-86 Mustang SVO used a unique K-member with specifically configured upper spring pockets and control-arm pivot provisions. (These models" K-frames were also fitted with Lincoln Continental forged lower control arms.)
OE K-frames are date-stamped (usually on the bottom) to indicate their year of manufacture. A typical (1987-93) production K-member weighs approximately 45 pounds. Depending on year and application, other OE Mustang K-frames tip the scales at as much as 57 pounds.
The Fox-body K-member physically dictates the shape of the OE V-8s" dual-sump oil pan. The separated front and rear sump sections are configured specifically to clear this crossmember.
Lightweight replacement K-frames (fabricated from steel tubing and weighing approximately 19 pounds) are available from aftermarket sources like Griggs Racing (800-655-0336). The Griggs K-member also carries FRPP part number M-5025-R1. FRPP carries a full line of lightweight Griggs suspension components for off-road Fox-body Mustangs. Lightweight replacement frame sections are regarded as being strictly competition-oriented.
Although the Mustang is not designed with any provisions to adjust front wheel caster, it is pos-sible to increase positive caster slightly by loosening the eight attaching bolts and moving the entire K-frame forward. This can allow as much as 1/4 inch of movement. But to be truly effective, all the mounting holes have to be elongated, and in all cases, the K-member must be precisely realigned. (Some of the attaching holes are already oval; others are round.) Relocating the K-frame in this manner pulls the front ball joints forward and improves static caster. It has the same effect as moving the struts" upper mounting points rearward. This modification also dictates revisions to the K-frame"s motor mount provisions to maintain the engine"s OE positioning.
The 1993 Cobra R-Model has its lower control arms" inner K-frame pivots repositioned further inboard (by .75-1.00 inch) to allow use of the slightly longer control arms from the 1994 SN-95 Mustang. Similar pivot-point revisions can be effected by welding steel plugs into the front control arm pivot/mounting holes and drilling repositioned pivot holes. This converts pre-1990 K-frames into the more advantageous later configuration.
Since the K-frame is a major load-bearing chassis member, numerous techniques have been developed to help deal with structure distortion under extreme conditions. In 1979, the earliest Fox Mustang K-frames were factory-fitted with additional diagonal bracing that tied the crossmember into the forward rocker sill area. This arrangement resembles one-half of the later convertibles" double-V-brace layout, described in Chapters 16 and 18. (The bolt-in and blind-riveted bracing is standard in 1983-and-later convertibles as well as in the 1993 Cobra R-Model.) The lightweight replacement Griggs K-frame does not require additional bracing. Non-OE K-frame modifications are described at the end of this chapter.
Motor Mounts
During the V-8 Fox cars" fifteen-year production run, the motor mounts have gone through numerous design and materials upgrades and changes. These include running revisions made to the mounts used on V-8 Mustangs built after October 1, 1980. V-8 Mustangs built after April 18, 1983, also received revised motor mount insulators and brackets.
The Mustang"s motor mounts are bonded steel-and-rubber assemblies used to locate and link the engine with the vehicle"s unitbody substructure. These units are also commonly referred to as engine mounts, insulator-and-bracket assemblies, or supports. Three motor mounts per V-8 car are used: one on the right side of the block, one on the left, and a third between the transmission (number three) crossmember and the transmission"s tailshaft housing.
Each of the rubber insulators (biscuits) has an embedded, threaded stud (two at the rear) to fasten the mount to the frame. The side biscuits use an embedded locating pin to position each insulator on the frame member it is attached to. The steel bracket bonded to each rubber biscuit has a pair of mounting holes for the bolts (and studs) that fasten them to the engine block and to the transmission case. Some Mustang models came with an extra stiffening brace between the right motor mount and the transmission case.
The rubber insulator biscuits on the two front mounts are fastened to the K-frame (number two crossmember); their attached brackets are bolted to either side of the engine block. The rear motor mount is supported on the transmission crossmember. (A special crossmember configuration is dictated by the 1986-and-later V-8 Mustang"s dual exhaust system.) All 1987-and-later production crossmembers can be used in a V-8 installation.
The transmission crossmember is supported between a pair of sleeved bushings, which, in turn, are carried on stamped-steel brackets welded to the underside of the floorpan. The fore-and-aft distance between these brackets on pre-1982 Mustangs and Capris, F-Zs, and the 1981-82 Granada/Monarch is 2.75 inches. All other Fox-body cars have mounting brackets 4.5 inches apart. FRPP offers a position-adjustable rear crossmember for Fox-body cars under part number M-5059-A.
Due mainly to the low-end torque output of the production five-oh, extended or severe service is hard on motor mounts. The V-8 rubber biscuit mounts deteriorate and lose their insulating and locating properties. Worn and/or separated mounts can cause problems with vibration, fan-to-radiator and fan-to-shroud clearance, operating linkages (including throttle, shifter, clutch, and AOD throttle valve cable action), over-angled driveline joints and splines, stressed wiring connections, exhaust leaks, underhood component interference, and even hood panel clearance problems.
To help limit excess engine movement and relieve the load on the production mounts, a solid torque strap (a cable and/or chain with an adjustable turnbuckle) can be used to secure the left side of the block to the frame. In street use, this competition-oriented arrangement will transmit considerable noise, vibration, and harshness to the rest of the vehicle but it takes a big load off the mounts.
Replacement motor mounts that have harder (and/or smaller) rubber biscuits or even solid aluminum blocks in place of conventional rubber biscuits are available from the aftermarket. One-piece solid mounts are also available from some of these same sources. The more rigid provisions will prevent excessive engine movement, particularly in severe service and/or competition applications. In exchange, rigid and solid mounts transfer more NVH from the powertrain to the cabin than production mounts do.
Front Control Arms
The Fox-body suspension design uses right and left lower control arms (A-arms or wishbones), but the system has no upper arms. The stamped-steel lower A-arms carry the ball joints and pivot on bushed through-bolts in the K-frame. Although the control arms" pivot positions in the K-frame were revised numerous times during the Fox-cars" fifteen-year production run (including notable changes for 1987-88 and 1990), all 1979-93 Mustang control arms are interchangeable, both left to right and year to year (except 1984-86 SVO models). All (non-SVO) Mustang front control arms measure 13 inches from the arm pivot center to the ball joint center.
Starting in the 1985 model year, Teflon-coated, low-friction ball joints were fitted in the GT and 5-liter LX standard Handling suspension system control arms and remained in Fox Mustang production through 1993. Designed to reduce bump impact harshness, these late joints can be identified by a distinctive lack of the grease fitting found on earlier, all-steel ball joints.
The 1987-and-later lower control arms are plated for additional rust resistance.
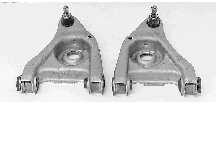
Fig. 29-2. A-shaped front lower control arms.
During the mid-1980s, Ford produced advantageous lower control arms for Fairmont police and taxi applications. These arms were stamped from thicker-gauge steel and are considerably stronger than their Mustang OE counterparts. Unfortunately, new replacements for these unique arms are no longer serviced by Ford.
Replacement control arms are available in kit form (including new bushings and low-friction ball joints) from FRPP under part number M-3075-A. Although some of Ford"s recent parts catalogs indicate different original equipment control arms for early and late Fox cars, the late version and the FRPP arms will fit all Mustangs except the (1984-86) SVO models.
For reference, an SVO Mustang front control arm is 1 inch longer than a Mustang arm (measured from the arm pivot center to the ball joint center). The physically interchangeable A-arm used on a 1987-88 V-8 Thunderbird measures 13.75 inches between its corresponding axes. (The slightly longer than OE T-Bird arms offer additional negative camber, but they also require more tire clearance. Although using T-Bird control arms does not require K-frame relocation or revisions to move the lower pivots inboard, these modifications are suggested.)
The original upper and lower control arms" forward bushings were formed hollow to help isolate road and axle vibration. These voided bushings improve ride characteristics but are too compliant for any sort of serious handling service. For 1989, the lower control arms" inner bushings were upgraded by Ford (in an unspecified manner). A front control arm bushing kit for 1985-95 Mustangs is available from FRPP. Part number M-3070-G1 includes quick-acting low-drag bushings with grease fittings, pivots and washers.
Note that a vehicle should always be positioned at its normal ride height whenever suspension bushings are installed and tightened in place. This avoids preloading the bushings and their suspension members. Noisy bushings can be treated with soap or marine grease to quiet their operation.
Year |
Outer (lb/in.) |
Inner (lb/in.) |
---|---|---|
1979-82 |
37,000 |
19,100 |
1983-93 |
21,500 |
15,700 |
1. Rates are shown as load in pounds per inch at a measured unit of deflection. |
Front Struts
The MacPherson strut was originally conceived (and patented) by Earle S. MacPherson in 1953 while he was working as Ford"s vice president of engineering At the time of its North American introduction on 1978 Fairmont and Zephyr
models, the MacPherson strut was considered the lightest, most basic, uncomplicated, and inexpensive independent suspension arrangement yet developed. It was also viewed as very advanced for a domestic automobile design. (At the time, MacPherson struts were typically used in small- and mid-sized European and Japanese imports. The Fox car"s modified version was developed by engineers at Ford of Europe.)
Front struts eliminate the need for upper control arms, upper arm pivots and supporting structures, and upper ball joints. This saves weight and complexity and provides numerous packaging advantages. The MacPherson strut design also makes it practical to incorporate a rack-and-pinion steering system and relatively compact tower structures (and upper mounts), which, in turn, contribute to the Fox car"s spacious engine bay. Ford"s modified MacPherson arrangement also allows for a generous range of wheel travel. As discussed previously the strut-based suspension arrangement also retains the use of conventional lower control arms.
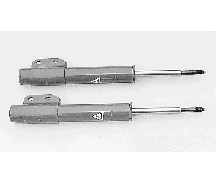
Fig. 29-3. Externally similar to all other production struts, these Koni units were used exclusively on the 1993 Cobra-R.
Ford"s 1979 Fox-body platform became the first production Mustang to use a strut-based suspension system. The front suspension is designed around a modified MacPherson strut that is less complex and less expensive to produce than a double-arm coil spring, leaf spring, or torsion bar arrangement. In the Fox MacPherson-based system, the shock/strut guides, damps, and limits wheel motion. The tubular strut cartridges also function as dampeners; the front shock absorbers are integral with the strut assembly. In its free state (out of a vehicle), the shock/strut has relatively low damping characteristics. But because these units are not vertical when installed in a car, they also carry side loads. Side loading increases damping resistance, because internal friction (sometimes referred to as "sticktion") is increased. The shock/strut"s outer housing (can) is free to rotate (relative to its internal piston"s connecting rod).
The Mustang"s strut design is referred to as "modified" because the coil springs are mounted separately from the struts. This allows more room in the engine bay around suspension and brake components. (In most common MacPherson layouts, the coil springs are wrapped around the strut cartridges.)
For 1984 1/2, low-pressure, gas-charged (nitrogen over oil) strut cartridges were put into Mustang service. Ford"s 1982 Lincoln Continental was the first domestic production passenger car model to use nitrogen-gas-filled shocks and MacPherson struts. In Lincoln-Mercury Capri applications, this arrangement was referred to as the Nitra-Cushion suspension.
Because these units apply a 100 psi nitrogen gas preload to their hydraulic fluid, they automatically extend to their full length when not installed in a vehicle. Approximately 50 pounds of force is required to manually compress the strut rod into the canister, which should not be confused with internal binding. The front cartridge struts are not serviceable; each must be replaced as a unit, and preferably in pairs.
Over the Fox Mustang"s production run, its struts" internal valving (mainly the metering orifices) was continuously retuned in efforts to optimize the cars" ride and handling. The strut tuning process also involved internal clearance settings, seal qualities, and bore and rod finishes.
Year |
Front cartridge (inches) |
---|---|
1979-86 |
1.375 |
1987-93 |
1.260 |
1. The piston diameter is slightly smaller than the external diameter of the can. |
The top mounts on the struts are carried by tower sections formed in the car"s stamped-steel unitbody shell. They are located underhood, in the engine bay"s fender aprons. The bottoms of the struts are attached to the front spindle carriers where they meet the outboard ends of the lower control arms. Both the struts and lower control arms are rubber-bushed at their attachment points. A rubber insulator and jounce bumper are used at the upper spring and strut attachment points.
Beginning in 1984 1/2, multipiece upper front strut mounts were employed (except in SVO
models). Although this later arrangement provides considerably more cushioning (to reduce noise and harshness) than the earlier one-piece "onion head" mounts, the multipiece mount is more flexible. In hard cornering, this excess play results in undesirable camber changes and more rapid tire-edge wear. For performance service, the early onion-type upper strut mount is considered superior to the late (1984 1/2-93) multipiece mount.
The 1987-93 struts" mounting flange ears at the bottom of the canister are approximately 1/8 inch closer together than on earlier struts.
For 1990, the tops of the front strut mounts were relocated slightly closer to the cowl. This revision increases the 1990-and-later Mustangs" nonadjustable caster setting by .63°, slightly reducing understeer and effecting more favorable wheel camber through a wider range of suspension travel.
Replacing OE and OE-like front struts with specially valved struts can improve a Mustang"s cornering characteristics or its ability to transfer weight rearward for maximum traction on hard acceleration. Because the mounting flange ears at the bottom of the early struts are approximately 1/8 inch further apart than on late struts, installing early (pre-1987) struts on a 1987-and-later Mustang requires aftermarket or custom spacers. Conversely, however, late (1987-93) struts will not work on a 1979-86 model. Some manufacturers include lower mount spacers with their replacement struts to give the units a complete range of Fox Mustang interchangeability. Using early struts on a late car will not have any effect on wheel camber, but the swap will reduce available suspension travel by 3/4 inch.
Replacing standard production (nonadjustable) upper strut mounts with slotted "caster/camber plates" from the aftermarket allows additional negative camber settings to be obtained as well as added positive caster. Installing aftermarket plates also replaces the rubber top bushing with a more positive bearing. Since the OE rubber bushing also functions as a noise attenuator (insulator), replacing it with a solid bearing increases ride harshness and noise transmission throughout the vehicle. Selective spacers fitted beneath the three top mounting studs can provide increased suspension travel and will also center the strut in mid-stroke.
Adjustable upper strut mount kits are available from FRPP for 1979-89 Mustangs under part number M-18183-G1 and for 1990-93 models under part number M-18183-G6. (For lowered 1990-93 Mustangs, FRPP kit number M-18183-G8 is specified.) If the production upper mounts are retained, the top bushings can be exchanged for firmer urethane replacements with only some of the solid mount NVH penalties. Replacement onion head mounts are available from FRPP under part number M-18183-H.
Front Springs
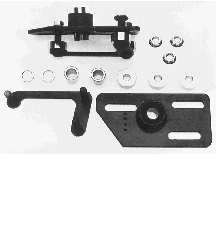
Fig. 29-4. Adjustable replacement upper strut mounts are also referred to as ?caster/camber? plates.
Helical-coil springs are used (front and rear) on all Fox-platform vehicles. Coil springs in a production Mustang"s suspension system are computer selected according to the specific equipment factory-fitted to each vehicle and how that equipment affects the car"s weight distribution.
All 1979-84 1/2 Mustangs were assembled with constant-rate (fixed- or linear-rate) front coil springs. Later (1984 1/2-93) V-8 Fox Mustangs are fitted with variable-rate (progressive-rate) front coil springs, which Ford calls "Vari-Rate" springs. A typical Mustang"s progressive-rate front coil spring measures 10.3 inches long by 3.5 inches in diameter. All 1979-93 non-V-8 Mustang base suspension systems (except the 1984-86 SVO models) use constant-rate, rather than variable-rate, coil springs.
Variable-rate coil springs become stiffer as they are compressed. Expressed in pounds per inch, the spring rate (deflection travel under a specific load or loads) increases progressively as applied loads increase. The more this type of coil is compressed, the higher the load required to compress it further. (In contrast, a constant-rate spring will compress the same distance under the same loads at all points in its normal operating range of travel.)
The Mustang"s progressive-rate springs are designed to compress relatively easily for their first 3/4 inch of travel. They then become progressively stiffer as they are compressed further. In an appropriately tuned system, this allows the suspension to deal best with conditions most commonly encountered in normal operation (on streets, roads, and interstates).
Compared to stiff (high-rate) constant-rate springs, variable-rate coils allow a controlled ride on rough roads and a smoother ride on smooth roads. Because of their progressive resistance to compression (and their relative ease of deflection during their initial segment of travel), variable-rate springs can produce a "jacking" (loading and unloading) effect during hard cornering. This means that ride quality aside, progressive-rate springs are not as effective for off-road performance service or competition as constant-rate springs.
Visually, the coils that form a constant-rate spring are equally spaced (vertically) along the entire height of the spring. A variable-rate coil is wound with varying coil-to-coil spacing. A front spring"s topmost coil is ground flat (to about one-half the wire"s original diameter) where its insulator seats in the K-frame. The bottom of a front spring"s coil terminates in a pronounced pigtail (wire end). On installation, the pigtail is positioned with its end between the two holes in the lower control arm"s spring pocket.
Most Mustang coil springs are wound from SAE 5160 steel. The wire from which a front coil is wound is much larger in diameter than the wire used to form a rear coil. Fox car front coil springs all use upper and lower rubber perch insulators to help reduce road noise transfer to the vehicle body and interior. Each spring uses a 1/2-inch-thick rubber biscuit between its top coil and the K-frame pocket and a split-tube rubber (wraparound) insulator between the bottom coil and the control arm perch.
Rubber isolator blocks (also referred to as internal rubber dampening sleeves or oscillation dampeners) are used inside the front and rear coil springs on 1984 1/2-and later 5-liter Mustangs as well as on those equipped with Handling suspension. These sleeves should be retained or replaced (but not eliminated) whenever the springs are changed.
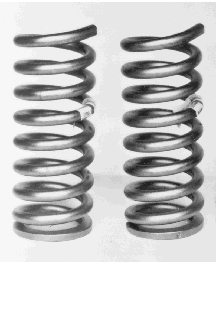
Fig. 29-5. Front springs
The lower right corner of a Mustang"s "data plate" door sticker contains a series of four single-digit code characters directly following a single-character transmission code. Typically expressed separately as front-and-rear, right-and-left designations, each character is keyed to the coil spring"s part number and spring rates. Translation keys to this coded data are published in each 1980-and-later Mustang"s service manual; some are explained further in dealer literature.
Year |
Rate type |
Spring rate (lb/in.) (1) |
||
---|---|---|---|---|
Standard/ |
Handling/ GT/ |
TRX |
||
1979 |
Constant |
370
|
395 |
425 |
1980-81 |
370 |
395 |
||
1982 |
395 |
410 |
||
1983-84 |
410 |
410 |
||
19841/2-86 |
Variable (2) |
425-525 (3) |
- |
|
1987-92 |
425-530 (3) |
- |
||
1993 |
400 |
425-530 (3, 4) |
- |
|
1993 Cobra-R |
Variable |
750-850 (3) |
- |
- |
1. Spring rates are expressed in pounds per inch and represent a coil stack"s nominal deflection rate. Non-V-8 rates are shown for comparison. 2. After approximately January 1, 1984, variable-rate springs came with the GT/Handling suspension system (standard with all V-8s). Constant-rate springs came with the base suspension system. Gas-pressurized (nitrogen-filled) struts were also introduced at this time (replacing the 1979-841/2 Mustangs" conventional air/oil hydraulic dampers). 3. The two numbers that express a variable spring"s rate indicate the normal ride height rate and the minimum coil height (full-jounce) rate. The first number is measured at normal ride height; the second is at full jounce. 4. Includes the 1993 Mustang Cobra . |
||||
It is important to note that removing a coil spring from a Mustang requires special equipment and techniques and should be attempted only by those with the proper tools and training. Appropriate cautions should be taken whether a spring is being removed for modification or for replacement.
Coil springs can be shortened in low-budget fashion by cutting winding sections from the coil stack. This can be accomplished by using a premium-quality hacksaw blade or a high-speed cutoff wheel (while the spring is off the car). This cut-and-try approach can be used to tune a spring/suspension system by experimentation. Shortening a coil spring"s height also increases its effective rate. The spring-shortening approach to lowering also allows the upper and lower spring insulators to be retained. (Front springs should be always be cut at the bottom, and rear springs at the top.)
Removing a spring"s rubber insulator biscuits can lower the front of the car (1/4-3/8 inch), but ride harshness, vibration, and metal-to-metal component wear will increase.
Nearly all Mustang coil springs are physically interchangeable within the 1979-93 Fox model line (although not front-to-rear), but not all springs are suitable for all mechanical combinations. The major exception to this situation involves the front springs in the 1984-86 Mustang SVO models. These unique coils are designed to suit those cars" longer lower control arms and compatibly canted upper spring pockets in the K-frame. Therefore, installing SVO springs in other Mustang models (and vice versa) is not a viable idea.
Lowering a Mustang by installing shorter springs will lower the car"s center of gravity and improve cornering ability, but this also limits weight transfer on acceleration and can hurt traction and straightaway elapsed times.
Replacement coils springs are available from aftermarket sources that include Baer Racing, Kenny Brown Performance, Central Coast Mustang, Eibach, Global West, JBA, FRPP, Steeda, and Suspension Techniques, among others. Note that many of these outlets also supply coil springs packaged with other select suspension components.
Front Stabilizer Bars
Link-type front stabilizer (anti-sway or anti-roll) bars are standard equipment on 1979-93 Mustang models. Stabilizer bars, especially the front bar, act as torsion bars to resist and limit body roll in corners. This increased roll stiffness, in turn, helps the tires remain as vertical as possible in relation to the road. (In a turn, body roll unloads the inside tires while loading the outside tires.)
The diameter of this solid steel bar is based on the engine and suspension options originally fitted at the factory. For 1985, the front stabilizer bar diameter on all 5-liter Mustangs was increased to 1.30 inches. This bar remained in service through 1993 and was also used on the 1993 Cobra R-Model. The 1993 Cobra uses a smaller-diameter front stabilizer bar (than the one used in the H.O. and 1993 Cobra-R), to increase the suspension system"s compliance and improve everyday ride quality.
Mustang front stabilizer bars are carried in rubber bushings (attached to the undersides of the front frame rails) and vertical end links fastened through the lower control arms. The earliest (1979-81) Fox-body models have a history of cracking problems that involve the upper front stabilizer"s mounting brackets. Redesigned brackets were released for 1982 production.
In straightaway acceleration, disconnecting a front stabilizer bar"s end links (at the track) can improve weight transfer by eliminating the binding action an anti-sway bar normally induces in the suspension system. A 1.30-inch-diameter stabilizer bar weighs 24 pounds.
Front stabilizer bars have early and late end-link designs. Early (1979-84) bars used rubber-bushed straight links with a spacer between each bar end and control arm. Later (1985-93) bars used shouldered end links (without spacers) between each bar end and control arm. The later links were also upgraded with Teflon-sleeved polyurethane bushings-inner, outer, top, and bottom. With a durometer rating of 82-85, these blue/green urethane bushings are the most favorable OE units to use with a 1.30-inch Mustang front bar. The Teflon sleeves reduce both friction and noise and are less compliant than the rubber units used previously. Although the late bushings" Teflon linings deteriorate in harsh and/or extended service, they are regarded as very effective handling enhancers.
A pair of the late links and their eight isolator bushings were specified under part number E6ZZ-5A486-A. Although this link-and-isolator package was revised after March 1991 (as part number F1ZZ-5A486-A), the earlier units will interchange.
It is generally agreed that little is gained in Mustang handling performance by installing larger-than-OE GT-diameter stabilizer bars. The 1993 Cobra"s smaller-than-H.O.-diameter front bar has proven effective with that car"s combination of more compliant suspension components and wider tires. The stabilizer bar kit listed in the FRPP catalog (under part number M-5627-A) includes an OE-type 1.30-inch front bar, Teflon-sleeved bushings, urethane link bushings, and an unbushed .79-inch rear stabilizer bar. For reference, 1994-and-later Fox-4 Mustangs are fitted with slightly lighter tubular steel stabilizer bars that are not directly interchangeable with the bars used on the earlier, Fox-body models.
Year |
Grade of solid steel |
Bar size (inches) |
Other |
||
---|---|---|---|---|---|
Standard/ |
Handling/ |
TRX |
|||
1979 |
SAE 1090 |
1.00 |
1.06 |
1.060 |
|
1980-82 |
.94 |
1.00 |
1.125 |
||
1983 |
1.125 |
||||
1984 |
1.125 |
1.20 (2) |
|||
1985-86 |
.94/1.125 |
1.30 |
- |
1.20 (2) |
|
1987 |
.94/1.125 |
|
|||
1988-93 |
.94 |
||||
1993 Cobra |
- |
1.125 |
|||
1993 Cobra-R |
1.30 |
- |
|||
1. Bar sizes are shown as diameter measured in inches. Non-V-8 sizes are shown for comparison. 2. This bar was used exclusively on the 1984-86 turbocharged four-cylinder Mustang SVO models. It is approximately 2 |
|||||
Rear Suspension
Ford"s 1979 Fox-body platform became the first production Mustang to use a coil spring rear suspension system. The Fox Mustang"s live rear axle assembly is suspended from the car"s rear longitudinal subframe rails on two coil springs. The rear axle assembly is located by four pivoting angled control arms, or trailing links. This arrangement is generally described as a live-axle, four-link rear suspension design. Ford referred to this as a "four-bar coil-link" arrangement.
Mustang V-8 cars (and the SVO and GT turbo fours) assembled for late-1984 were equipped with the Quadra-Shock rear suspension system, which replaced the earlier (1982-84 1/2) V-8 Mustang"s twin traction-bar arrangement as axle locating control links. For 1984 1/2, the rear suspension"s upper pivot points (on the subframe rails) were lowered 1/2 inch, and the lower body pivot points were lowered 1/4 inch. This effectively lowered the car"s rear roll center. Gas-pressurized rear shock absorbers (and gas-filled front struts) also debuted for 1984 1/2.
The 1993 Cobra"s softer (than a GT) constant rate rear springs, smaller-than-standard-diameter front stabilizer bar, and 17-inch tires improved ride and handling in that car"s combination of more compliant suspension components. The 1993 Cobra R-Model is equipped with competition-oriented, variable-rate rear coil springs.
Ford developed a new independent rear suspension system for the 1999 Cobra. The IRS shares common "hard points" with non-IRS Mustangs, but it is not a bolt-in replacement for a 1979-99 rigid OE axle. Modifications also have to made to the fuel tank, fuel filler, brake lines and to the driveshaft.
Rear Control Arms
Two pair of upper and lower trailing arms are used to locate and control a Fox Mustang"s rear end. Rear control arms are rubber bushed and attach to the vehicle via upper and lower brackets mounted on the rear subframe rail stubs. (Upper arm brackets are on the rails" inboard faces; lower arm brackets are on the outboard faces.)
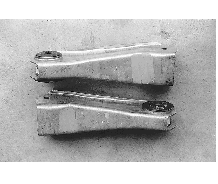
Fig. 29-6. Upper control arms.
A pair of short upper trailing arms are positioned between the subframe rails and the upper sides of the rear end"s cast-iron center section. These arms are angled laterally to help locate the axle housing, side-to-side. In severe and/or extended service, the forward attaching frame rail brackets on the rear upper control arms have been known to deteriorate and create either loose or failed joints at those connections. (Using harder-than-OE polyurethane replacement bushings at this point only makes matters worse.) To help strengthen these stressed connections, the brackets can be mig welded and/or bolted to the frame and/or the adjacent floorpan.
All 1979-93 production Mustang upper rear control arms are interchangeable. Starting in mid-year 1992, Special Service Mustangs were factory-fitted with specific upper control arms. Identification-marked by a blue paint daub, these upgraded arms also feature revised-spec, fully bonded bushings. FRPP replacement arms (part number M-5500-A for all 1979-93 Fox cars) feature harder (than OE) bushings. Replacement upper control arms offered by Hotchkis Performance feature boxed construction and urethane bushings
Two longer lower trailing arms are positioned in brackets under the outboard ends of the axle tubes to manage the axle housing"s forward and rearward movement. The front pivots on the arms are carried in torque box structures tied to the outboard faces of the subframe rails just forward of the rear wheels. The Mustang"s standard rear stabilizer bar also functions to keep the lower control arms parallel, especially under hard acceleration.
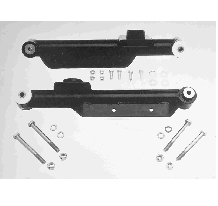
Fig. 29-7. Replacement lower rear control arms.
All 1979-93 production Mustang lower rear control arms are interchangeable. Super Duty replacement lower control arms from FRPP (part number M-5649-A) have spherical, Teflon-lined front bushings and grease fittings for the bushings in the rear end housing. Aftermarket replacement control arms (from sources like Griggs, Chassis Engineering, Edelbrock, HP Performance Products, Maximum Motorsports, Southside Machine, and Steeda) offer features like boxed channels, an adjustable spring seat, polyurethane bushings, and adjustable ends. Replacement lower arms fabricated from boxed aluminum are also available from the aftermarket, for obvious structural advantages. Boxed aluminum arms also offer an unsprung weight saving of approximately 2.5 pounds (per pair). Both types are typically packaged with extra-duty bushings. Some replacement arms are configured to allow more room than stock arms for offset wheels and wide tires.
Access to the arms" forward pivot bolts in the torque boxes may be obstructed by exhaust system components in some applications.
A production Fox Mustang"s four-link rear suspension system contains eight rubber pivot-point bushings. Steel pins inserted in the bushings at the factory are used to tune each rubber mounting cushion for its specific application. The factory bushings used in rear control arms (and stabilizer bars) are made of rubber that is too soft for serious performance service. This excessive compliance allows them to compress too easily under load to properly locate and control the rear axle assembly during hard driving maneuvers. In contrast, a bushing that is too hard can cause suspension links to bind and limit suspension action and control.
Some of these OE bushings" deflection load ratings are shown on the accompanying chart. Complete production data on the subject of OE suspension bushings remains elusive. Until more complete specifications are uncovered, the numbers shown should be regarded as reference figures only.
|
Body bushing rate (lb/in.) |
Axle bushing rate (lb/in.) |
||
---|---|---|---|---|
Year |
Upper |
Lower |
Upper |
Lower |
1979 |
13,000 |
12,000 |
9,800 |
17,000 |
1982 |
13,000 |
19,000 |
24,000 |
|
1983 |
8,700 |
19,000 |
24,000 |
|
1984-93 |
8,700 |
10,000 |
9,900 |
16,000 |
1. Rates are shown as load in pounds per inch at a measured unit of deflection. |
For 1984 1/2 (through 1993), the lower rear control arms" round front (frame-end) bushings in (non-SVO) Quadra-Shock cars were replaced by new, oval bushings. The oval bushings reduce ride harshness because they allow some fore-and-aft movement of the rear end when sharp road-surface irregularities are encountered. This added rear-end housing movement is handled by the Quadra Shock setup"s horizontal dampers. Despite the added horizontal shocks, oval bushings are not practical for serious performance service because of the extra play their deflection allows. (The Quadra-Shock-equipped late-1984, 1985 and 1986 Mustang SVO models retained the early, round bushings.)
In mid-1992, Special Service (police) Mustangs were assembled with new upper control arms and revised-spec, fully bonded bushings. These "poured-in-place" bushings are described as being firmer than standard and as having a durometer rating between those of an OE Mustang GT and the much less resilient FRPP bushings. Fully bonded bushings are fabricated by pouring hot rubber into a mold formed by the bushing"s inner and outer steel sleeves (as opposed to being pressed and shrink-fitted within these two metal cylinders). Bonded control arm bushings were also used on the 1993 Mustang Cobra.
Through approximately 1983, a Mustang"s rear upper control arms" forward pivots were assembled with eccentric bushings and sleeves designed to permit adjustment of the rear end"s pinion angle. The rear bushings in the upper arms are part of the rear end, rather than being integrated into the arms themselves. The pinion angle is set (in relation to the ground) with the vehicle at rest to produce minimal universal-joint angularity (at the driveshaft-to-rear-end junction) under the full range of suspension travel. Maintaining a proper angle becomes particularly critical during hard cornering and under acceleration and deceleration.
When servicing Mustangs built after the early-eighties, adjusting the pinion angle requires installation of Ford"s service, or replacement, control arms, which come fitted with the adjustable eccentric bushings. The early-OE and replacement adjustable bushings contain an offset inner through-bolt sleeve, typically situated at the "six o"clock" position (viewed end-on). Increasing the pinion angle requires rotating the bushing in the control arm counterclockwise. Decreasing the pinion angle requires clockwise rotation. The bushing orientation in both right and left upper arms must match.
For performance service a 2° negative (nose-down) pinion angle is considered optimum. Adding aftermarket traction control devices often alters the pinion angle drastically and should be compensated for.
The eccentric bushings were discontinued as original equipment when Ford found other ways to maintain properly controlled pinion angle tolerances in production while using conventional concentric bushings. Eliminating the adjustability feature also eliminates the possibility of improper settings being made in the field.
Year |
Rear end size (inches) |
Pinion angle |
Curb height (inches) (1) |
---|---|---|---|
1979-81 |
7.5 |
3° 18´ (± .5°) |
5.07 |
1982-85 |
7.5 |
2° 27´ (± .5°) |
5.07 |
1986-93 |
8.8 |
.48° (± .5°) |
4.49 |
1. Curb height is measured between the top of a rear axle"s housing tube and the bottom of the jounce bumper bracket attached to the outboard face of the rear subframe rail above that axle tube. |
Replacement bushings are available from the aftermarket in molded rubber and plastic compounds as well as solid aluminum. Although aftermarket suspension sources initially offered round bushings only, oval replacement bushings eventually became available for the 1984 1/2-and-later Fox models. The 1993 Cobra uses specific rear control arm bushings.
Replacement rear upper control arm bushings from FRPP are included in an 8.8-inch axle installation kit, part number M-4050-B. This package also contains a pair of axle C-clips and 4 ounces of friction modifier additive for the rear end lube.
On installation, suspension bushings should be tightened in place only when the vehicle is positioned at its normal ride height. This avoids preloading the bushings and their suspension members.
Rear Springs
The rear coil springs are carried between rubber insulator biscuits on the rear end"s lower control arms on the bottom and on rubber insulator biscuits on brackets attached to the outboard faces of the rear frame rail stubs (just forward of the kickup areas) at the top. Removing these rubber insulator biscuits will have the same effect it has up front.
A rear coil spring"s outside diameter visibly tapers down toward its bottom. On installation, a rear coil spring"s lower pigtail should be positioned at the rear of its seat, pointing toward the left side of the car. A typical Mustang"s variable-rate rear coil spring measures 8.7 inches by 4.00 inches in diameter.
The 1993 Cobra came with constant rate rear coils. The 1993 Cobra-R"s variable-rate Eibach rear springs are unique among Fox Mustangs. Selected primarily for their suitability in "showroom-stock-style" endurance road-race competition (under 1993-94 rules), the R-Model springs are shorter than other OE Mustang coil springs. In the 1993 Cobra-R, they help lower the car by approximately 3/4 inch.
Other than these differences, the descriptive data for the rear springs is the same as that given earlier in this chapter for the front springs.
Year |
Rate |
Spring rate (1) |
||
---|---|---|---|---|
Standard/ |
Handling/ |
TRX |
||
1979-84 1/2 |
Constant |
160 |
160 |
175 |
1984 1/2-93 |
Variable (2) |
160 |
200-300 (3) |
- |
1993 Cobra |
Constant |
- |
160 (4) |
|
1993 Cobra-R |
Variable |
240-260 |
- |
|
1. Spring rates are expressed in pounds per inch and represent a coil stack"s nominal deflection rate. Non-V-8 rates are shown for comparison. 2. After approximately January 1, 1984, the GT/Handling suspension system that is standard with V-8s was upgraded with variable-rate springs. Constant-rate coils were retained in the non-V-8 Mustang"s base suspension system. 3. The two numbers that express a variable spring"s rate indicate the normal ride height rate and the minimum coil height (full-jounce) rate. The first number is measured at normal ride height, the second at full jounce. 4. Constant-rate rear springs are used in the 1993 Cobra model and in 2.3-liter Mustangs equipped with the base suspension only. |
||||
The sources and numerous details and precautions in the Front Springs section also apply to identifying, modifying and replacing a Mustang"s rear springs.
Traction Bars
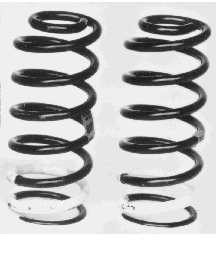
Fig. 29-8. Rear springs.
For 1982-83 and part of 1984, pre-Quadra-Shock Mustangs in GT (and SVO) trim or those equipped with the GT package and the 5-liter H.O. V-8 were assembled with two extra gusseted rear suspension links. These members were designed to act as slapper-type traction (anti-tramp) arms and are also referred to as "traction bars" and "hop bars." U-bolted to the outboard bottom of the rear-end housing, each link (one per side) carries a cylindrical rubber sleeve. This bumper is positioned to contact a striker plate (bolted to the underside of the lower control arm) when the rear-end housing rotates (as the suspension compresses during acceleration, cornering, etc.).
In production, the links are shimmed to produce an air gap. Factory specs call for adjustment shims stacked to create a 1/4-3/4-inch gap (with the static vehicle at curb height). This gap can be tightened to zero to stiffen rear-end movement and somewhat limit axle hop. Tight settings in this area are also known to create unusual loading problems in hard cornering situations. This is due to an imbalanced increase in the effective rate of the rear coil spring on the side of the car that is on the outside of the turn. In tight corners, this prevents load transfer to that tire and subsequently promotes wheelspin. The OE traction bars are known to get hung up on wash racks, and they also weigh more than the Quadra-Shock setup that replaced them. In March 1983, Ford issued a Technical Service Bulletin covering traction bar settings and service.
Replacement traction bars from the aftermarket can overstress and crack the Mustang"s unitbody structure in the torque box area at the rear of each rocker panel. (In severe service, even torque boxes without add-on traction devices are overstressed.)
Rear Shock Absorbers
Although Fox Mustangs use hydraulic strut cartridge dampeners in front instead of the more conventional shock absorbers, every Fox Mustang comes with at least two rear shock absorbers per car. Some Mustangs (Quadra-Shock-equipped) are fitted with four shocks per car. Fox body designers splayed the rear frame subsections (body rails) to accommodate vertical rear shocks mounted outboard of the rails. All 1979-93 OE shocks have 1-inch-diameter pistons.
Mustang shocks underwent constant revisions before and after the mid-1984 introduction of the Quadra-Shock system. Over the Fox Mustang"s fifteen-year production run, its shock absorber"s internal calibrations (mainly the metering orifices) were continuously retuned in efforts to optimize the car"s ride and handling. As with the front struts, the tuning process also involved internal clearance settings, seal qualities, and bore and rod finishes.
Ford"s Quadra-Shock rear dampener arrangement was initially developed as part of an upgraded suspension system to support an "improved-performance 5-liter engine" program. A complete upgrade package had originally been planned for release at mid-year 1984. But when that engine-based equipment group was delayed until the 1985 model year, only some late-1984 cars were fitted with all the suspension upgrades that had been planned. As a result, Ford"s Quadra-Shock rear suspension arrangement was fitted to the limited-production late-1984 Mustang SVOs and many standard production V-8 (and turbo-four GT) Mustangs built after mid-year 1984. For 1985, the Quadra-Shock system entered full production on all V-8 Mustangs as well as on those equipped with the GT/Handling suspension option. (Following their Fall 1984 intro, delivery of 1985 V-8 Mustangs to dealers and their customers was delayed.)
The four-rear-shock-absorber Quadra-Shock arrangement features two dampeners at each end of the rear axle. One shock per side is oriented vertically, and the other horizontally. The multi-shock setup was designed to help control axle hop (torsional axle oscillation) on hard acceleration and to stabilize transitory handling by absorbing the twisting action of the rear-end housing without restricting suspension travel.
The Quadra-Shock system replaced the dual traction-bar setup used on 1982-84 Mustangs equipped with the 5-liter V-8 (and on early-1984 SVOs). The Quadra-Shock arrangement weighs slightly less than the traction bar system. The horizontal rear shock arrangement was also used on 1985-86 SVO models. These handling-oriented Mustangs came with Koni dampeners exclusively. (Koni"s were also fitted to the 1993 Mustang Cobra R-Model.)
Thunderbirds built for 1987-88 and equipped with the Sport Handling package and non-IRS Turbo Coupes also came with a Quadra-Shock rear suspension system.
One pair of telescoping, double-acting hydraulic dampers are mounted vertically behind the axle housing. ("Double-acting" means that the shock"s valving regulates fluid flow between internal chambers on both damper jounce (compression) and rebound (extension).) The lower ends of these shocks are bolted to the same outboard brackets on the axle tubes that the lower control arms use for their rear pivots.
On non-Quadra-Shock models, the shocks lower pivot bolts are oriented longitudinally (fore-and-aft). The lower pivot bolts on Quadra-Shock rear vertical shocks are turned 90°. Positioning these pivots laterally (in standard Quadra-Shock fashion) helps limit binding when the axle housing twists on acceleration and deceleration. The tops of the vertical shocks are attached to brackets mounted to the outboard faces of the rear frame rail stubs in their kickup areas. Access to the top mounts is gained through interior wheelhouse panels with a 15 mm socket wrench.
Starting in 1984 1/2, all shocks and struts were nitrogen-gas-pressurized. The 1993 Cobra retains the production Quadra-Shock arrangement. The 1993 Mustang Cobra"s optimized shock valving has proven very effective with that car"s combination of more compliant suspension components. The 1993 Cobra R-Model is equipped with adjustable Koni rear shock absorbers rather than the standard nonadjustable Tokicos found on other 5-liter models.
The Quadra-Shock arrangement adds a pair of freon-gas-cell- (gas-bag-) equipped horizontal dampeners to the rear suspension system. Designed to resist rear suspension compression, or axle "windup," the trailing shock bodies mount between brackets on the top rear of the axle housing tubes and brackets to the rear of the axle, on the outboard faces of the subframe rails. The horizontal pair of gas-over-oil dampeners by Gabriel /Maremont are also referred to as "kicker shocks," or "kickers."
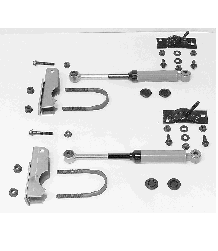
Fig. 29-9. The components in this FRPP bolt-on quad-shock kit help illustrate the OE system's basic layout.
In acceleration-oriented straightaway applications, large tires can create clearance problems between the tires and the horizontal pair of Quadra-Shocks. Although these kickers can be moved inboard slightly for extra tire clearance, many competitors remove them completely to make room for 9.5- and 10.5-inch extra-wide race-type rubber. In extra-high-horsepower applications, removing the horizontal shocks dictates the addition of special locating/control members (and/or bushings) to help manage the Mustang"s live rear axle.
Quadra-Shocks can be retrofitted to 1979-84 V-8 Mustangs and to later models built without them. Brackets are required on the rear axle and frame to accept Quadra-Shocks. Starting in early 1984, the four-shock-absorber arrangement was offered in bolt-on kit form by FRPP under part number M-4263-C. The FRPP kit includes a template for proper positioning, but drilling access holes in the trunk and bolt holes in the frame to accept the shock mounts can be difficult and time-consuming. The axle housing brackets should also be tack-welded in place.
In service, Mustangs that were not Quadra-Shock-equipped tend to develop sloppy lower shock mounts. These cars can be retrofitted with the sturdier lower mounting bracket and pivot arrangement that came on Quadra-Shock models (fastened to the rear faces of the lower control arm mounts on the axle tubes). The Quadra-Shock mount also offers a more advantageously oriented lateral pivot layout, but this later mounting setup also requires appropriately configured vertical shocks. A number of different lower shock bushing eye widths (on the vertical dampers) were used in Mustang production.
Replacement shock absorbers from the aftermarket are offered for both vertical and horizontal dampers.
Rear Stabilizer Bars
A rear stabilizer (anti-sway or anti-roll) bar was factory-fitted to all V-8 Mustangs. The diameter of this solid steel lateral link was based on the engine and suspension options ordered on a particular car. Isolated from the body, the linkless U-shaped transverse steel bar is attached directly between the (1982-93) rear end"s lower control arms. A typical .79-inch-diameter solid steel rear bar weighs 10 pounds.
A rear bar helps limit body roll, which, in turn, helps the tires remain as vertical as possible in relation to the road. Excess body roll can also create undercar clearance concerns as well as uncomfortable driving conditions.
Because the solidly mounted bar resists travel, it functions as a lateral constraint member rather than as an anti-roll bar and relieves some of the load on the springs. When the proper rear stabilizer bar (rate) is fitted, softer rear springs can be particularly effective.
On-track testing has indicated that (on certain courses) a stock V-8 Fox Mustang will corner equally well and will clock similar lap times without a rear stabilizer bar. In straightaway applications, removing the rear bar (to save a few pounds) is not recommended, because it helps locate the lower control arms and keep them parallel under acceleration.
Because the 1979-81 stabilizer rear bar was redesigned for 1982, fitting a 1982-and-later rear bar to a 1979-81 Fox car requires redrilling the mounting holes in the lower control arms. The 1994-and-later Fox-4 Mustangs are fitted with slightly lighter tubular steel stabilizer bars that will not interchange directly with earlier, Fox-body models. Larger (.9375-inch and 1.00-inch-diameter) rear stabilizer bars are available from the aftermarket.
Year |
Grade of solid steel |
Bar diameter (inches) |
|||
---|---|---|---|---|---|
Standard/ |
GT/ |
TRX |
Other |
||
1979 (9) |
SAE 1090 |
(2) |
.50 |
.56 |
- |
1980-81 (9) |
.50 |
.56 (4) |
|||
1982-83 |
.56 |
(7) |
|||
1984 |
.67 |
.56 |
(3, 8) |
||
1984 1/2-85 |
.79 |
- |
.67 (3) .83 (5) |
||
1986 |
.67 (3) .83 (6) |
||||
1987-93 |
SAE 5160 |
.83 (6, 10) |
|||
1. Bar sizes are shown as diameter measured in inches. Non-V-8 bars are shown for comparison. 2. The Mustang"s base-level suspension is not designed for use with a rear stabilizer bar. 3. This bar was used exclusively in 1984-86 on the turbocharged four-cylinder Mustang SVO models. 4. Standard only with the 2.3-liter turbomotor when ordered along with the TRX option. 5. With Special Handling and GT/Handling suspension systems. 6. Standard with the GT and 5-liter LX models" Handling 7. Available mid-year 1983 with a .067-inch bar in the GT/Handling suspension 8. Available mid-year 1984 with a .079-inch bar in the GT/Handling suspension. 9. The 1979-81 stabilizer rear bar was redesigned for 1982. 10. Includes the 1993 Mustang Cobra and the 1993 Cobra |
|||||
Pinion Snubber
For 1985-93, 5-liter Mustangs equipped with the T-5 transmission were fitted with a rubber pinion snubber and bracket attached to the underside of the floorpan. The snubber and an axle-mounted striker plate prevent direct floorpan-to-rear-end contact on suspension compression.
A replacement pinion snubber and bracket assembly is shown in FRPP"s catalog under part number M-4905-A. Installing a taller-than-OE pinion bumper can help stabilize the rear axle on hard acceleration. By cutting back on suspension travel in this manner, the snubber also helps maintain acceptable pinion angles.
Because the Cobra-R"s lower ride height increases the possibility of contact between the pinion snubber and the rear-end striker, the standard production snubber was trimmed by approximately 1.5 inches.
Replacement adjustable pinion snubbers are available from aftermarket sources.
Suspension and Frame
Modifications
Under high dynamic loads (fast cornering, full-throttle acceleration, enthusiastic gear changes, and/or hard braking, for example), Mustang frame sections are known to flex unacceptably. The Fox car"s minimal floorpan and roof structures allow excessive flexibility, especially along the car"s longitudinal axis. Further flex loads are also applied by the Mustang"s high-performance powertrain and the extreme motoring conditions to which many of these vehicles are subjected. Note that some of the bracing arrangements described here may interfere with the installation of long-tube and/or equal-length headers.
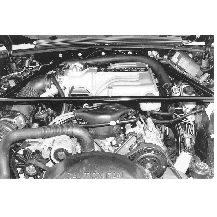
Fig. 29-10. Adding strut-towers-to-firewall bracing can help stiffen the front end and the entire car.
Add-On Bracing
Adding a 1993 R-Model-style triangulating strut-tower-to-cowl "export" brace can help stiffen the front-end structure as well as the entire car. Since the Mustang"s cowl/firewall area is not particularly sturdy, a triangulating engine-bay brace should be further supported with a base plate attached at its mounting point on the cowl/firewall structure. Similar base plates are also suggested at both strut tower connections.
A strut tower (upper) crossbrace for 1979-93 Mustangs is listed in the FRPP catalog under part number M-20201-A50. These braces are also available from other aftermarket sources, including BBK, Jamex, and Maier Racing.
Adding a transverse member (a lateral steel tube commonly referred to as a G-load brace or lower chassis brace) across the bottom of the K-frame legs (near the rear of the lower control arm pivots) can also help stabilize a Fox car"s heavily loaded suspension and engine mounting structures. The most common type of these aftermarket lower chassis braces is a two-point member. Other aftermarket setups connect to the car at four points. Adding a transverse member between the front frame rail stubs helps tie the substructures together and also helps support the K-frame itself. Maximum Motorsport"s lower brace provides a direct path for suspension loads.
Starting in 1983, production convertibles were fitted with an undercar crossbrace that ties the K-frame to the subframe at points fore and aft of that number two crossmember. This bracing is also standard in the 1993 Cobra R-Model. A pair of OE-style V-braces are included as part of FRPP"s Chassis Stiffening Kit (part number M-5024-A). The FRPP kit contains the same basic braces, reinforcing plates, and fasteners (bolts and rivets) used by Cars and Concepts to finish the Mustang convertibles they produced for Ford.
The aftermarket offers a steel-tube lateral brace that connects the rear shock towers to help stiffen that section of the Mustang"s stamped unitbody. In a hatchback, this arrangement intrudes on interior cargo space.
Installing welded-in subframe connectors is one of the most effective changes that can be made to any Fox-body Mustang, so much so that adding connectors is strongly suggested, even before any major powertrain upgrades are made. Adding longitudinal braces along the rocker panels between the front and rear subframe stubs will help those stamped structural sections develop added stiffness, especially when the engine"s output levels are elevated.
Although bolt-in subframe connectors for 1979-93 Mustangs are available from FRPP under part number M-5478-B, it is strongly suggested that these members be welded to the subframe stubs. Attaching them by drilling holes and using threaded fasteners can, in some installations, hurt overall structural integrity rather than help it. FRPP also offers "double-cross" subframe connectors under part number M-5478-J. Configured to distribute dynamic loads over more of the body structure, these braces are designed to be welded in place.
Chassis Welding
When adding any sort of stiffening or support braces to improve chassis characteristics, welding always offers structural advantages over conventional threaded fastener connections. Keep in mind that permanent welded-in additions like those discussed here can also limit access to other components and systems. Among the more common front subframe modifications is full-bead welding of all the K-frame"s factory-tack-welded seams and those between the torque boxes, floorpan, and frame rails.
The torque boxes formed on the underbody of V-8 Mustangs are identical to those on a four-cylinder model. These sections of stamped sheet metal that form the Mustang"s unitbody in the areas where the lower rear control arms are attached are known to distort under load. Because they are tack-welded to the underside of the floorpan (immediately forward of the rear wheelhouses), the floorpan can also become distorted and the factory welds can fail in severe and/or long-term service.
When severe service is planned, steel reinforcements and welded seams offer durability improvements. At least one aftermarket source (Wild Rides) offers a torque box reinforcement kit. To strengthen the stressed connections where the rear upper control arms are attached to the subframe rails, the mounting brackets can be mig welded and/or bolted to the frame and/or floorpan.
Ford issued Technical Service Bulletins (in May 1990 and April 1991) advising owners and service shops about potential problems with the EEC processor due to arc welding. These notifications suggest that the battery"s ground cable be disconnected whenever arc welding is done on a car with computer-managed engine controls. Ford had also released a Technical Service Bulletin in June 1983 covering specific procedures for welding the Mustang"s high-strength, low-alloy steel (HSLA) chassis and body sections. Always follow common sense safety precautions when welding, especially around fuel and electrical equipment as well as near trim, bushings and other structural software.